Why You Should Use Shellac on Your Weissenborn Guitar
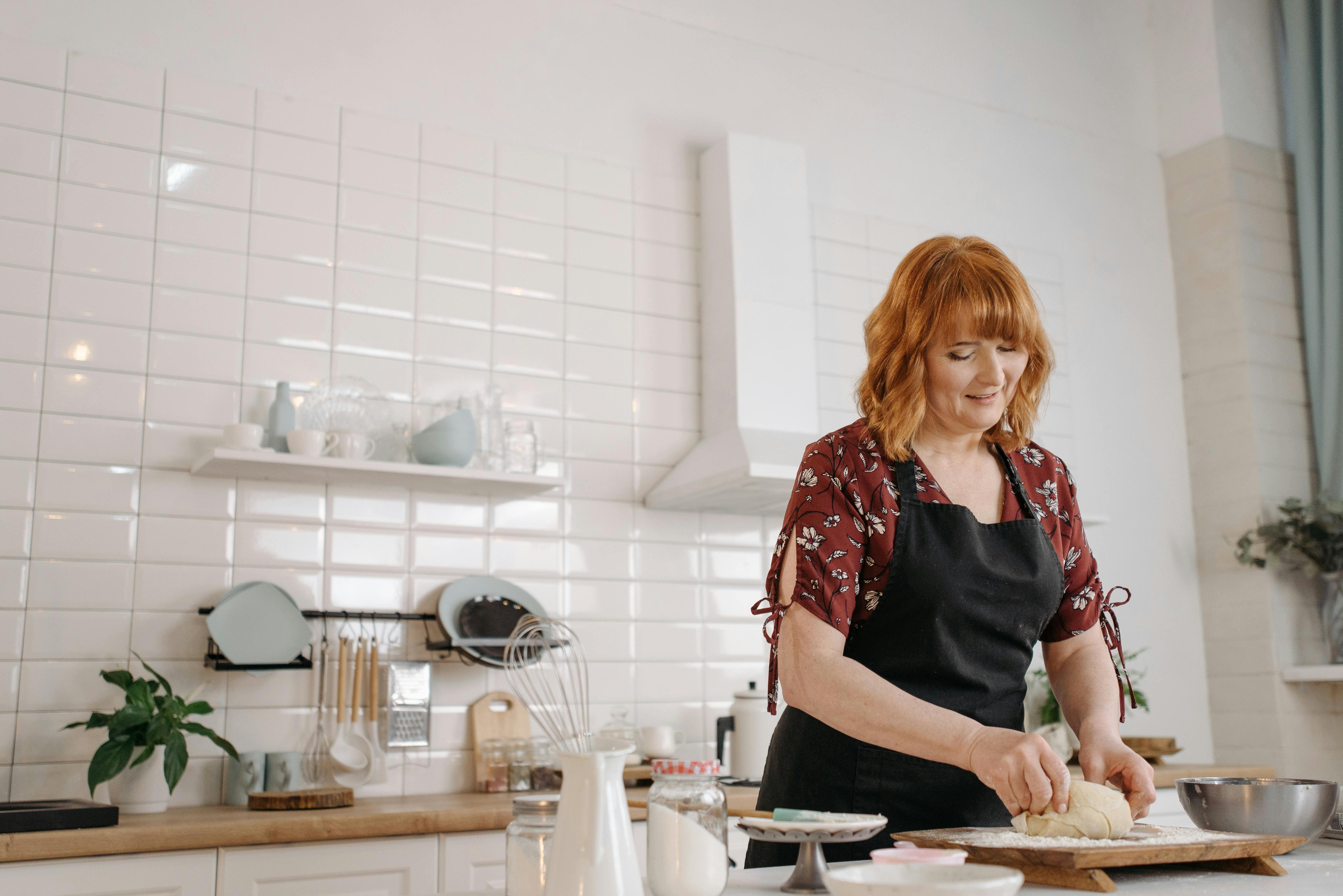
When I started building my Queensland Maple Weissenborn guitar, I almost immediately started thinking about what kind of finish it was going to have. To be completely honest, I had really decided early on that it would be a Shellac or “French Polish” finish.
The maple was extremely strong and very lightweight with a beautiful flamed finish and there was no way I was going to contemplate drowning it in some thick, gooey man-made goo that would kill every twang and overtone these rich, vibrant guitars produce. I had used shellac before on several vintage guitars and one of my favorite guitars in particular, a 1967 Levin Goliath, had been coated with white shellac, another variant of polishing. The sound of this recently converted forty-five year old lap steel guitar has to be heard to be believed.
TRADITIONAL FINISH
Shellac and alcohol based finishes have been in use since the early 18th century and have stood the test of time. It has the advantage of being simple to prepare, non-toxic, and apart from methyl alcohols, most of which evaporate into the atmosphere, chemical-free. It is a natural product derived from the secrets of a South American beetle and is collected by hand from the trees where the beetle lives and ends up in the form of dried flakes and is dissolved in methylated spirits or alcohol (two pounds per gallon) and stirred well until thick consistency.
It is applied in a number of ways, by hand with a cotton ball wrapped in a soft, lint-free cloth known as “gum”, brushed fine, or even sprayed onto the wood.
It does, however, have an Achilles heel and application techniques must be mastered before an acceptable finish can be achieved. In this worldwide rush where many arts and skills must be mastered, many people do not have the patience to persevere in learning and move on to the easier methods of applying guitar finishes.
Once some initial success has been achieved, the frustrations of hand polishing shellac on a quality guitar, and the great sounds it helps produce, will be quickly forgotten.
WHY USE SHELLAC?
There are many reasons why shellac is a favorite of many luthiers. The application technique, once mastered, can be astounding and in the hands of an expert it can look exactly as if it had been sprayed with the highest quality lacquer.
However, the main reason I personally prefer it is because shellac, once applied, dries almost instantly and when multiple coats have been applied it is extra light with a beautiful sheen that allows all the natural timbre and nuances to come through. of the soundwoods vibrate freely and allow the rich fullness of the sound to be released. It is no coincidence that many of the incredible qualities of the beautiful and unique Stradivarius violins have been made using shellac, although the exact formula is still unknown.
Shellac also has other endearing qualities. Many shades of wood stains can be mixed with Shellac to produce a wide variety of wood colors, but still retain transparency to allow the grain pattern to show through.
The amazing natural orange shellac color is bursting with brilliance and appears to glow and smolder, setting the wood on fire with an alluring glow.
APPLICATION OF SHELLAC
There are generally two preferred methods of applying shellac, one known as padding and brushing.
Using a soft, natural-hair Chinese brush, the shellac should be brushed off with long, fast strokes. Shellac will dry almost instantly, leading many people to think it’s impossible to get a decent finish. However, perseverance is required and the secret is to never re-brush the previous pass until it has completely dried. If you brush again while the first coat is still wet, the half-dry shellac will simply tear and smudge when the ‘sticky’ brush picks up the previous coat. At first, a lot of patience is required! Also, since the mix is often very thin, it is not unusual to have to apply twenty or more coats until the coating is even enough to achieve a reasonable coat.
The second method, apparently preferred by many, is the padding method. However, it is the more difficult of the two methods and will not be learned in an hour or two. Constant and regular practice will allow confidence to grow and the results may surprise you!
There are some preferred and seemingly unorthodox methods of constructing a ‘pad’. The idea is to wrap a soft liner (or shell) of soft material (like a clean cotton sock) with a ten-inch square (give or take!) of lint-free cotton muslin. The muslin is formed into a ball with the free material twisted into a “handle” and the ball is dipped into the shellac-alcohol mixture and applied in a long, even motion onto the wood.
It is good at this stage to point out a few tips: Do not allow the inner pad to ‘flood’ with excess shellac… shellac can dry so quickly that the ‘pad’ can drag or stick to the surface of the wood. …a compromise must be achieved… to help do this, a small container of clean, light mineral oil can help considerably by lubricating the pad as it travels. Dip in the oil, then in the shellac and repeat the stroke. It has been compared to an airplane taking off and landing!
ENDING!
Again, there are a few different methods in use. One is to coat, let dry, and use 400 grit (very fine) sandpaper to sand the dried coat, remove the fine chalky white powder residue, and recoat…then the whole process is repeated . Others will apply a few coats and then sand the job down.
Once the desired number of coats is applied (no real number here, but at least 5-10 coats) the entire piece is allowed to dry for at least 24 hours. Direct application of many coats will result in a high gloss, mirror-like finish, but many people prefer to rub the work with 0000 finishing steel wool to remove any “tips” and then buff with a non-silicone wax polish until smooth. a high gloss. .
If a satin type finish is required, simply buff with 0000 grade steel wool and buff very lightly!
If you liked this article and want to read more, there is more detailed information in another article called Advanced Polishing Techniques in French by the same author.
Terry Buddell, the author is an enthusiastic and competent writer of many similar articles which can be found on his website http://www.buildaweissenborn.com where many other articles and the book and CD of plans are available to build a Weissenborn from high quality. You can find acoustic lap steel guitars.