Worm Parts Grinding Crack Reason Analysis
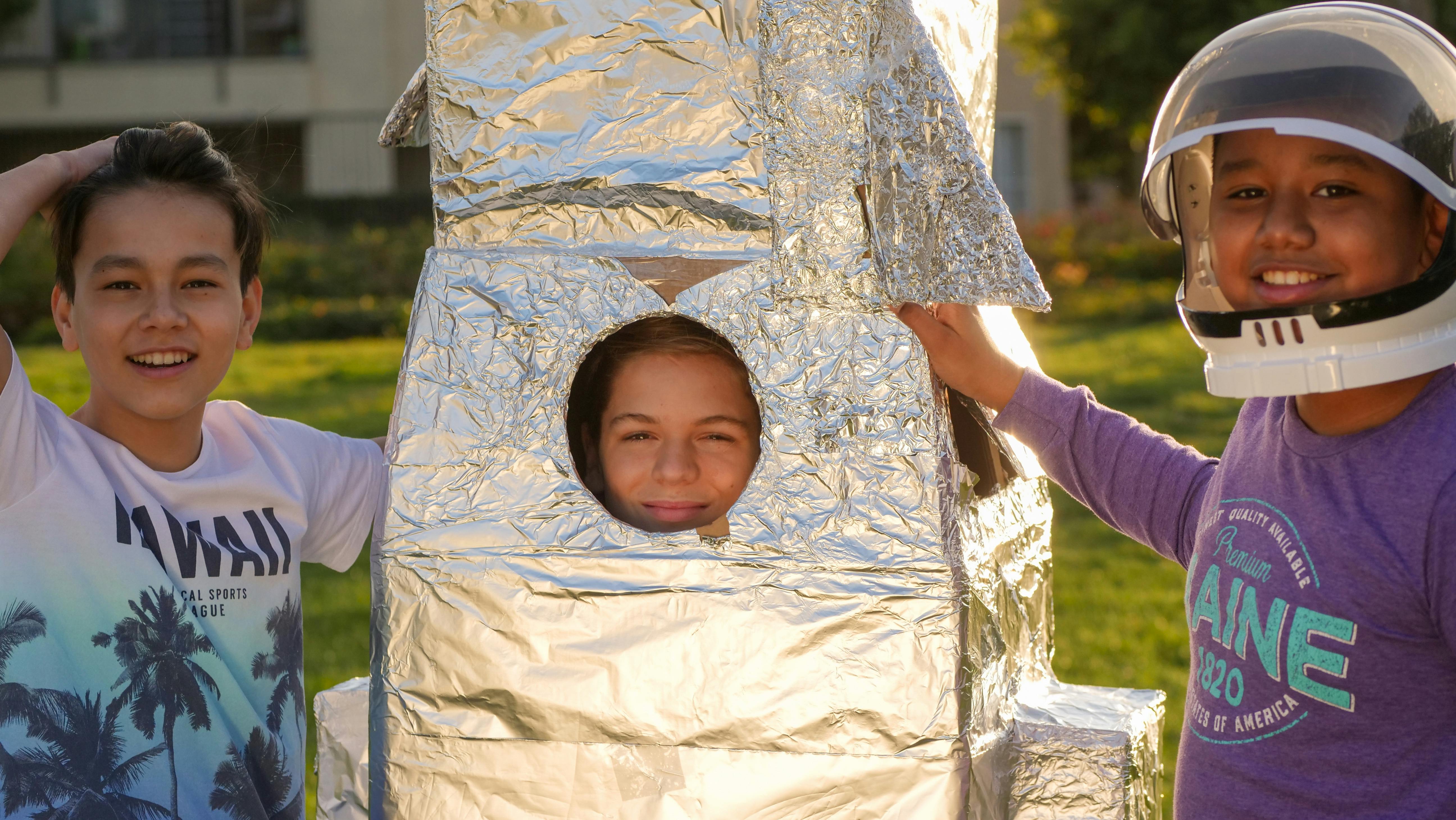
The worm is an important part of the rotating parts of the machine tool. The spiral surface of the worm and the tooth surface of the worm gear are relatively slippery when working, which is easy to use. Therefore, the worm will usually receive quenching treatment to obtain higher hardness and prevent wear on the spiral surface of the worm. Worm parts require high precision, so the processing technology is complex and long. If there is any problem during the processing, it will cause a big loss. A kind of worm parts in our company appeared cracks during grinding, resulting in scrap parts, which seriously affected the production schedule.
1. Worm material and main process flow
The worm material is 20CrMnTiH and the heat treatment requires case hardening and quenching with a depth of 1.1-1.5mm and a surface hardness of 58HRC after quenching.
Blanking→Forging→Tormalizing→Rough machining→Stress relieving→Fine machining→Carburizing→Thread carbon removal→Quenching→Rough grinding→Testing→Aging→Fine grinding
Heat treatment process: Normalizing forging → Carburizing → Quenching → Low temperature quenching → Smoothing → Stress relieving → Low temperature aging.
After carburizing and tempering, the carburized layer depth is 1.32mm and the surface hardness is 59 to 60HRC.
2. Description of the crack phenomenon
After rough polishing, the crack appears on the surface of the worm tooth. The cracks are very fine, linear and shallow. The shape of the cracks is usually called a “hairline”. The cracks are not parallel, scattered lines.
3. Analysis of grinding cracks
It is obviously different from common cooling cracks. The cooling cracks are thick and deep, and the number of cracks is small. It only occurs on the grinding surface, and the number is large, the depth is shallow, but the depth is basically the same. The clearest are cracks in stripes perpendicular or nearly perpendicular to the grinding direction. The surface of the worm tooth is a spiral surface.
In the grinding process of heat-treated parts, the instantaneous high temperature in the grinding zone can reach 400-1500℃ because the grinding wheel is blunt, the grinding depth is too deep, and the cooling is insufficient. As a result, grinding burn occurs, resulting in changes in the surface microstructure, microhardness, residual stress, and mechanical properties of parts.
The formation of cracks is related to the hardness of the work piece. Although the workpiece with hardness less than 55HRC may burn, the occurrence of grinding cracks is rare. Workpiece with hardness higher than 60HRC will greatly increase the possibility of cracking. The measured hardness of the workpiece is 59 ~ 60HRC, which greatly increases the tendency of grinding cracks. On the one hand, when the grinding conditions are unsuitable or the grinding is non-standard, the grinding surface will first form a strong burning center, resulting in uneven thermal stress. In alternating high temperature and rapid cooling, the voltage value gradually increased. When the stress exceeds the resistance limit of the material, the surface of the floor will produce cracks. On the other hand, the austenite retained in the carburized surface and the quenched structure will be transformed into new martensite by the influence of intense grinding heat and coolant cooling during grinding, which will cause local volume expansion on the surface of the grinding. part. increase tensile stress on the part surface and lead to stress concentration. Continuous grinding will easily accelerate the generation of grinding cracks.
From the above analysis, we know that the root cause of grinding cracks lies in the existence of stress. To prevent this phenomenon, it is necessary to reduce and eliminate various stresses on the surface of the parts.
Welcome visit our website: http://www.hy-inductionheater.com/